In 2009, TANN Corporation designed and installed a 320,000 SCFM RTO system for a medium density fiber board plant. The exhaust stream from the wood process is highly corrosive and contains a substantial amount of particulate. Because of this, most RTOs require frequent and expensive maintenance to the flow control valves, ceramic media, and the media support. TANN’s custom approach to the process exhaust has provided an incredibly reliable RTO system for the customer over the last 9 years.
Design Advantages:
- Random packed media design to reduce the effects of fouling
- Reliable & low maintenance poppet valves
- No gaskets or seals to replace
- Bake-out capability
- High destruction efficiency
- High thermal efficiency results in lower operating costs
- Stainless steel plate construction
- Elevated tank design for cold face accessibility
- Induced draft fans, with additional static pressure to overcome system fouling
Update 2019
After almost 9 years of operation, the 320,000 SCFM RTO system is operating as expected. The system is inspected annually by TANN Corporation and a media bake out is conducted to burn off the organic build up in the media beds and media support. Over the life of the system there has only been minor maintenance conducted on the internal insulation and poppet valve components, saving the customer over $1,000,000 in valve/damper maintenance and media replacement compared to other systems.
Project Photos
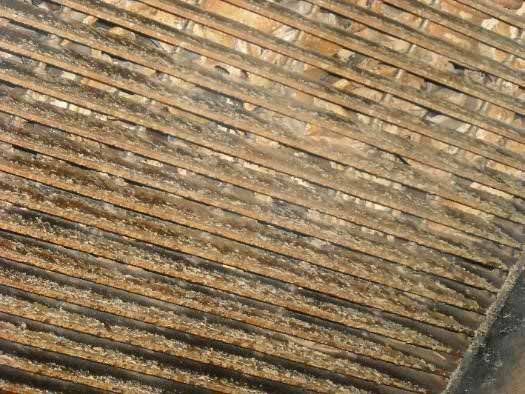
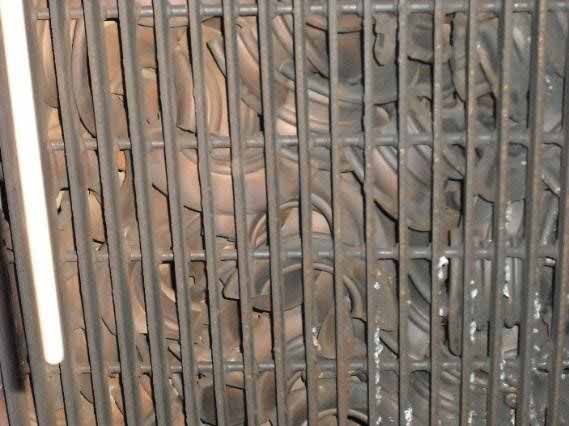